The tire pyrolysis equipment is aimed at converting waste tires into oil by utilizing high temperature heating and special catalyst. This green technology (called pyrolysis) is proved to be an ideal method to solve the issue of waste tires pollution. The following is a simple description of tire pyrolysis process:
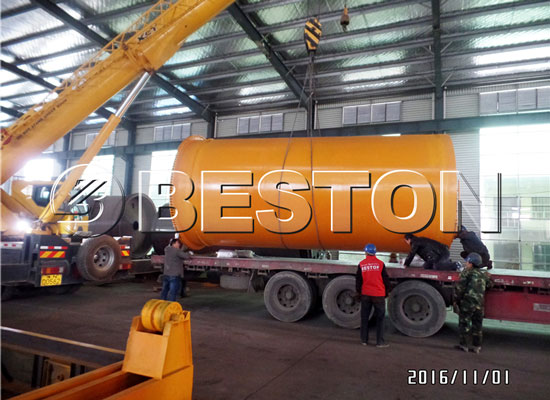
1. Feed raw materials
Feed the waste tires into reactor and make reactor rotate clockwise 0.4-0.8r/min. Seal the feeding inlet door tightly and make sure there is no gas leakage.
2. Pyrolysis
Heat the reactor by using coal, charcoal, fuel gas, wood etc. as heating materials. The reactor will be slowly heated, and when the temperature reach about 250℃, the oil gas will be formed.
3. Condensing
The oil gas coming out from the reactor then go to condensing system and get liquid oil. We adopt new-type condenser which can improve the oil yield efficiency and make the oil yield to the maximum.
4. Waste gas recovery
The gas which can’t be liquefied under normal pressure will be designed to go back to combustion system through safety device. It can be recycled to heat the reactor as fuel, which will save energy for the whole working process.
5. Discharge
After finishing oil production, the temperature of the reactor will be cooled down, when the temperature falls down to 40℃, we can discharge the carbon black and steel wire.
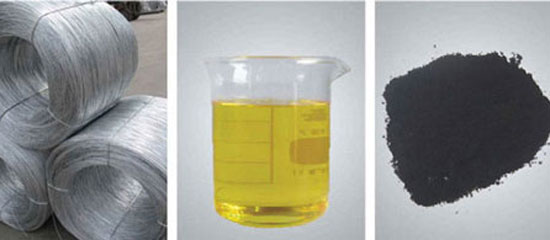
This is the basic procedure of tire to oil recycling process. But due to different operating systems of the tire recycle plant, batch, semi-continuous and fully continuous, the tyre to oil process differs from three aspects.
Firstly, before feeding raw materials, continuous operating systems need a shredder machine to cut tires into small pieces (30-50mm), while batch system doesn’t need this pretreatment.
Secondly, for the continuous systems, the feeding of materials and discharging of carbon black are both automatic, while for the batching system, the two processes are manual.
Thirdly, the fully continuous system can work 24 hours per day without a stop; the semi-continuous system can work 3-4 shifts per day and it only needs one hour to cool the reactor before the second batch; While the batch system can only work one shift per day, and it needs 5-6 hours to cool the reactor.
Model | BLJ-6 | BLJ-10 | BLJ-16 | BLL-20 |
Daily Capacity | 6T | 8T-10T | 15-20T | 20-24T |
Working Method | Batch | Semi-Continuous | Fully Continuous | |
Raw Materials | Waste Tyre, Rubber, Plastic, Oil Sludge | |||
Reactor Size | D2.2*L6.0m | D2.6*L6.6m | D2.8*L7.1m | D1.4*L11m |
Pattern | Horizontal & Rotary | |||
Heating Materials | Charcoal, Wood, Fuel Oil, Natural Gas, LPG, etc. | |||
Total Power | 24kw/h | 30kw/h | 54kw/h | 71.4kw/h |
Floor Area (L*W*H) | 30*10*8m | 30*10*8m | 40*10*8m | 45*25*10m |
Operating Pressure | Normal Pressure | Constant Pressure | ||
Cooling Method | Water Cooling | |||
Life Span | 5-8 Years |