With the increasing consumption of plastic products, waste plastics are also increasing rapidly. At present, China’s waste plastics mainly come from plastic film, plastic foam, plastic packing box and container, plastic bags, discarded medical equipment, etc. In addition, China’s annual consumption of plastic has reached 400 thousand tons; electronic appliances and household appliances with plastic consumption has reached about 1000000 tons. These products have become one of the most important sources of waste plastics. If they are handled improperly in the process of storage, transportation, processing and applications, it is bound to damage the environment and will harm the health of people. So in order to deal with the waste plastic in a green and profitable way, Beston has developed the waste plastic pyrolysis recycling plant.
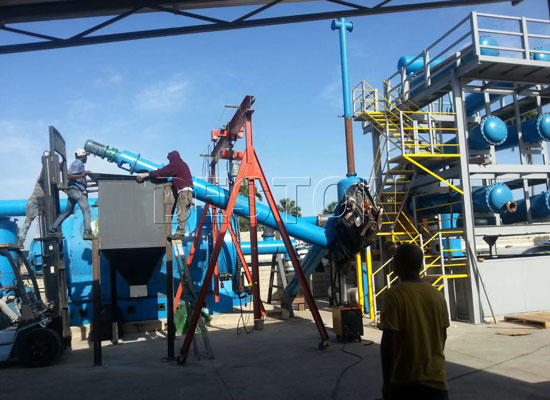
Final products from plastic pyrolysis
The plant takes advantage of one advanced technology called pyrolysis, which refers to heating waste plastics and special catalyst in the reactor by high temperature (about 250-280℃). Through the efficient plastic pyrolysis process, we can get crude oil and carbon black. Both of the end-products are in high demand and can sell well in the market. The crude oil can be widely used in industries such as steel and iron factories, ceramics, power or chemical industries etc. The carbon black can be used for construction bricks with clay, also can be used as fuel.
Pyrolysis process
1. Put dried raw material into reactor by full-automatic feeding machine, then it is delivered into stock bin by conveyer belt. Oil gas will be generated when the temperature inside reactor reaches 100℃. Then sealed door for feeding shall be closed. After that, open the heating system.
2. From 100 degree celsius to 250 degree celsius is the preliminary stage. The light oil gas shall be released at 100 ℃ and fluid oil shall be released at 120 degree celsius. From 250 to 280 degree Celsius, oil gas will be separated from the Oil gas and collected into slag oil tank. The lighter gas will rise up to the multifunctional oil condensers, be liquefied into oil and stored in the oil tank. The incondensable gas through desulfuration and dedusting by hydroseal will be led to the reactor for recycling.
3. Cool down the reactor before make sure all above mentioned has been done. Carbon black will be discharged when the temperature reaches at 40 degree Celsius.
1. High-caliber and professionally engineered safety components like a pressure gauge and an automatic warning device.
2. The auto feeding system that helps reduce extra need for manual operations and enhance the plant’s productivity.
3. Effective exhaust gas and waste water processing and releasing systems. This ensures all the used gas and waste water are emitted in the desirable state that can’t harm the atmosphere.
4. Well sealing for heating system and specific operating tech to heating which can improve the output rate by 5%.
5. The exhaust gas will be recycled for reactor heating, so this system will enable you don’t need to add fuel.