Beston has high-quality tire recycling equipment for sale now, which can convert waste plastics into pyrolysis oil, carbon black and steel wire without causing secondary pollution. The tire recycling equipment mainly includes batch operating plant, semi automatic operating plant and fully automatic operating plant. The following are some differences between the batch and fully continuous systems:
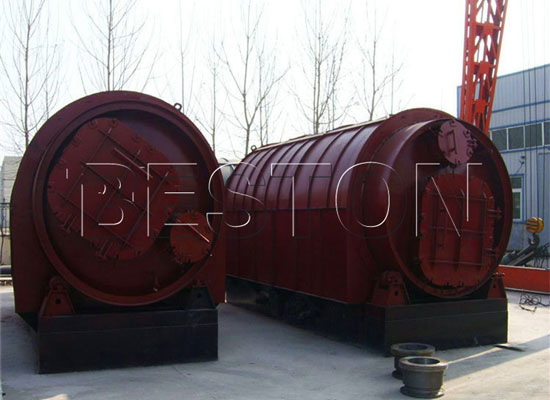
Firstly, the continuous pyrolysis system needs a tire crusher to cut the tires into small pieces (30-50mm). While the batch pyrolysis system doesn’t need pre-treatment devices and the tires can be put into the reactor directly. Secondly, for the continuous pyrolysis system, its feeding of tire and discharging of slag are both automatic. While for the batch pyrolysis system, its feeding process and discharging of steel wire are both manual. Thirdly, the continuous pyrolysis system can work continuously for 24 hours per day without a stop. The semi-continuous plant can work 3-4 shifts per day and only needs one hour to cool down the reactor before the second batch. While for the batch pyrolysis system, it can work one shift per day and needs 5-6 hours to cool down the reactor.
No matter which set of tyre recycling equipment you choose, you will get high quality guarantee. Our each set of equipment is certified by CE, ISO, SGS. The following are the advantages of our equipment:
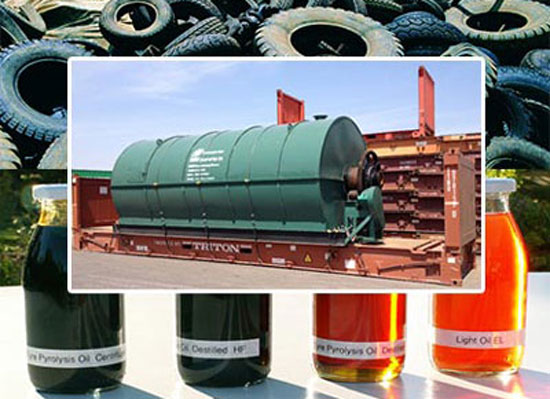
1. Safe.
1) Totally sealed pyrolysis process, so the gas will not leak and danger can be avoided.
2) It is equipped with mature safety devices (alarm for over temperature and pressure, auto pressure releasing system, extra gas recycling system, fire fighting devices), which can guarantee 100% safety in the production process.
2. Energy-saving.
1) The latest heating method which can not only save fuel but also prolong service life of the reactor.
2) The exhaust gas will be recycled by the extra gas recycling system, which saves energy and reduces pollution.
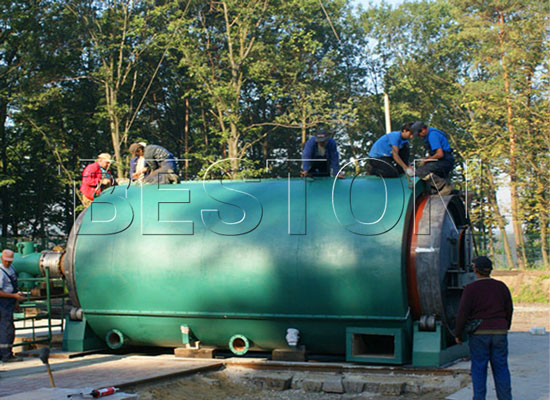
3. Environmental protection.
1) It can discharge slag in a totally sealed environment and the working environment can be greatly improved.
2) Advanced dedusting system (water spray, ceramic ring filter, washing chamber) to guarantee the released gas is pollution-free.
Item | Details | |||||
Model | BLJ-6 | BLJ-10 | BLL-16 | BLL-30 | BLL-40 | BLL-50 |
Daily capacity | 6T | 10T | 20T | 30T | 40T | 50T |
Working method | Batch | Semi-continuous | Fully continuous | |||
Raw materials | Waste tire, plastic, rubber, oil sludge, medical waste | |||||
Reactor size | D2.2*L 5.1m | D2.8*L6.2 m | D2.8 *L7.1 m | L12.5*W2.2*H2.5m | ||
Pattern | Horizontal & rotary | Not rotary type | ||||
Heating materials | Charcoal, wood, fuel oil, natural gas, LPG, etc. | |||||
Total power | 24 kw/h | 30 kw/h | 54 kw/h | 53.6kw/h | 62kw/h | 84kw/h |
Floor area (L*W*H) | 20*10*10 m | 25*15*10 m | 25*15*10 m | 20*15*10m | 33*15*10m | 33*15*10m |
Operating pressure | Normal pressure | Constant pressure | ||||
Cooling method | Water cooling | |||||
Service life | 5-8 years |